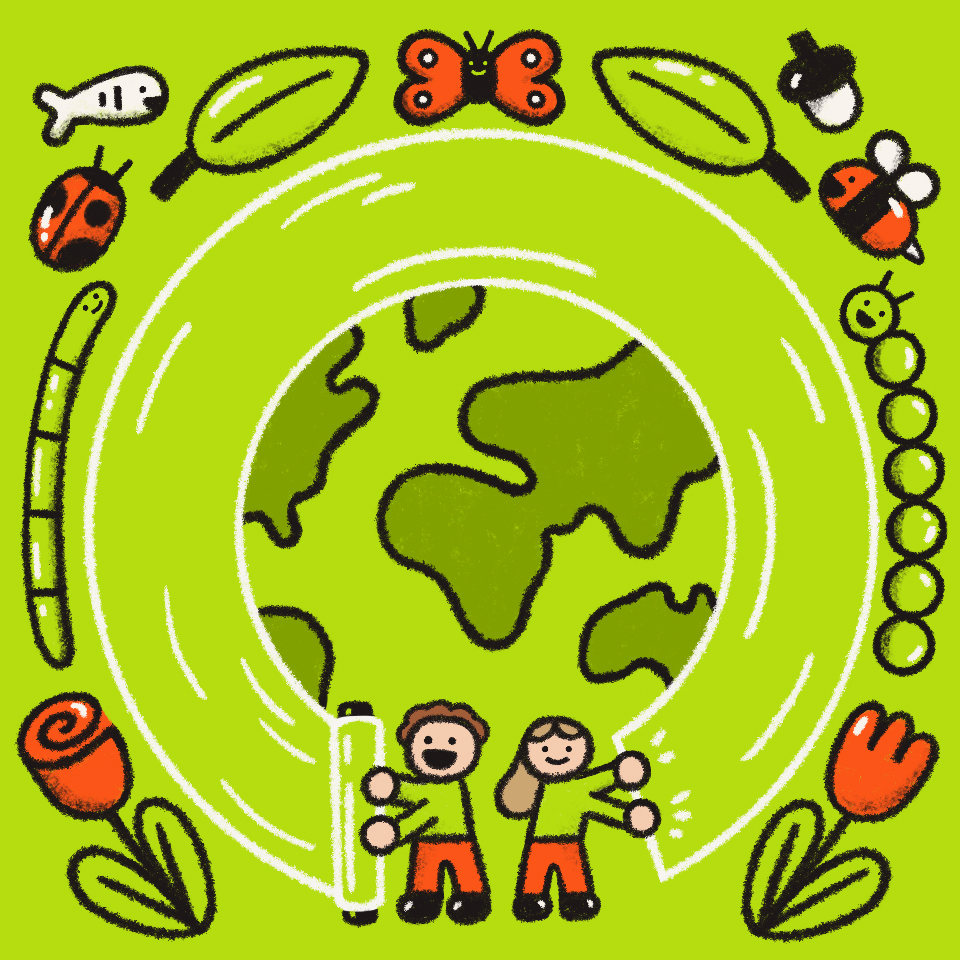
How Great Wrap is eliminating plastic waste, one roll at a time
Published on September 20, 2024
This Australian company wants to end humanity’s reliance on plastics in 10 years. They’re using Dropbox and DocSend to help them stay efficient and secure funding for that goal.
Here’s a not-very-fun-at-all bit of trivia for you: Humans have produced 8.3 billion tons of plastic—and half of that was just produced in the last 13 years, according to the United Nations.
Out of that, only 9% is recycled; the vast majority ends up in landfills (72% per MIT) while the rest gets incinerated, dumped into the ocean, or ingested. (The U.N. estimates we eat a credit-card worth of plastic every week. Cool.)
“[To] paint a picture of the scale of the problem,” Julia Kay says. “Every piece of plastic that's ever been made still exists… This is a multi-faceted problem that is going to take a lot of different solutions to solve.”
If Julia and Jordy Kay have their way, plastic will be replaced with compostable alternatives in the next decade. To that end, the Kays and their team have invented Great Wrap, the only compostable hand and machine pallet wrap made in Australia.
Unlike plastic or biodegradable wrap (which, respectively, can take 20-500 years or 3-6 months to decompose into toxic byproducts), Great Wrap is made from compostable biopolymers and plant-based oils that break down into carbon and water in 180 days in an industrial compost facility—faster than an orange peel. It’s also affordable and stronger than traditional plastic, Kay says, a feat five years in the making.
“No,” she says, laughing when asked if they have any competitors. “No one’s crazy enough.”
The company’s growth has been swift and organic, reflecting its founders’ love story. Julia and her husband Jordy met in 2019 at a Melbourne rooftop bar and connected over their interest in wine, sustainability, and design. In three months, they would register the name “Great Wrap”; a year later, they launched the business and their marriage.
Since then the Kays have sold hundreds of thousands of meters of Great Wrap in Australia, and expanded into the U.S. in 2022. They’ve designed a MoMA-worthy cling-wrap dispenser made from 33 plastic bottles (of course); built a devoted fan base; and raised $29.1 million in funding by selling investors on their vision for a plastic-free world.
“We had no idea in the early days that we were going to end up with a huge manufacturing facility, our team, investors, and everything that comes along with being a startup,” Kay says while driving to the aforementioned space. “It was really just something we were exploring.”
As Great Wrap went from pipe dream to reality, the Kays needed tools to help them meet the scale of the problem they were solving. Dropbox and DocSend became crucial partners in that effort.
From wine to wrap
Plastic pollution is a worldwide issue, but as Aussies, Julia and Jordy are especially invested: In 2021, The Sydney Morning Herald reported “Australians generate more single-use plastic waste per capita than any other country in the world.”
They saw plastic pollution on the beach and at work—Jordy, as a natural winemaker, and Julia, as an architect. It was demoralizing, working so hard to make eco-friendly wines and buildings only to be undercut by shipping. Sure the vino is biodynamic and the building materials are sustainably sourced, but if the pallets they arrive in are covered in plastic wrap, did it matter?
The couple wanted to create an alternative with a completely circular and unproblematic life cycle. Something that could be just as cost-effective, flexible, and strong as traditional stretch wrap, but that could break down into organic matter instead of microplastics.
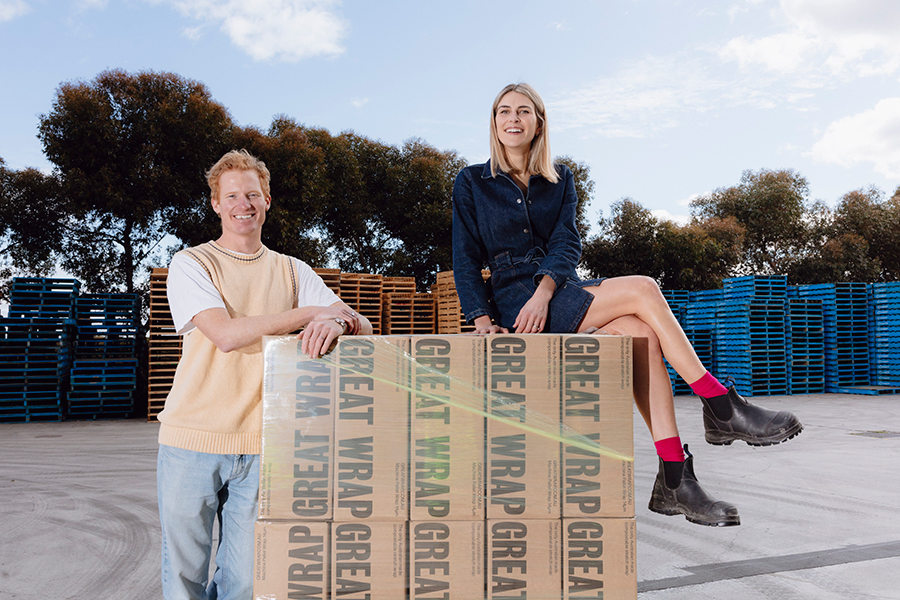
"You get nervous when you’re getting something out into the market: Do people think it’s important?"
While Julia and Jordy had technical backgrounds, they weren’t in the material sciences. As luck (or fate) would have it, they knew someone who was: Eddie Attenborough, a scientist and PhD candidate at Monash University.
Attenborough brought in Monash University’s chemical engineering team to help research and develop Great Wrap. But first, they needed to see if the market was even interested in a compostable pallet wrap. After eight months, they found a contract manufacturer to partner with for an initial product.
“You get nervous when you’re getting something out into the market: Do people think it’s important? Is this a meaningful problem to solve?” Kay recalls wondering.
They didn’t have to wait long for an answer. Within hours of setting up their website and Instagram account, Great Wrap had messages from Australian and international airports and wineries. Their entire inventory sold out in a day.
Securing a plastic-free future
The demand for compostable pallet wrap was clear: They were shipping out $100,000 worth of pre-orders from their living room. And after 12 months of tinkering, the team found a mix of 10 biopolymers that, when heated up, can be transformed into Great Wrap and smells like...
“How can I describe it?” Kay pauses. “It’s kind of like… if you’ve opened up a packet of plain chips, and then there’s a slightly toasted one in there, with a hint of popcorn.” (Is it edible? “It’s been through a polymerization process so that it acts exactly like plastic. So… wouldn’t recommend it!”)
Those beads are then transformed into odorless, transparent, and compostable pallet wrap. To ensure it actually ends up in compost bins instead of landfills, the team created a digital aftercare kit. Customers get a link to a Dropbox folder that holds a cache of technical data sheets, product specifications… all the things high-volume businesses need to know about industrial composting.
When the pandemic hit, Great Wrap launched another product in response: cling wrap, a little something for all the cooks and gardeners at home during lockdowns. As orders came in, so did a recurring question: Why wasn’t Great Wrap made in Australia?
“To see that so many people cared was the motivation we needed to go out, set up the factory, and start to do this at scale,” Kay says now.
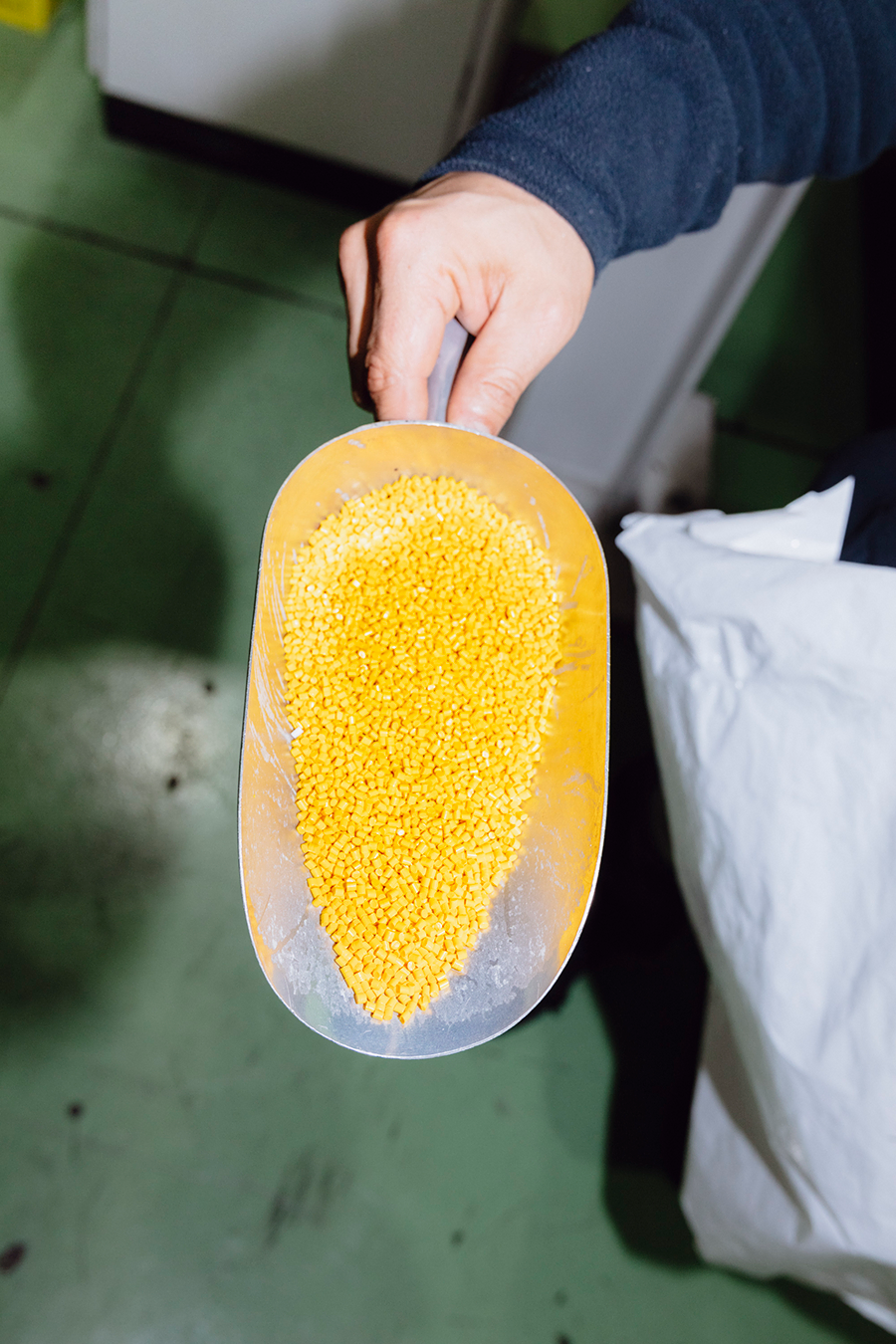
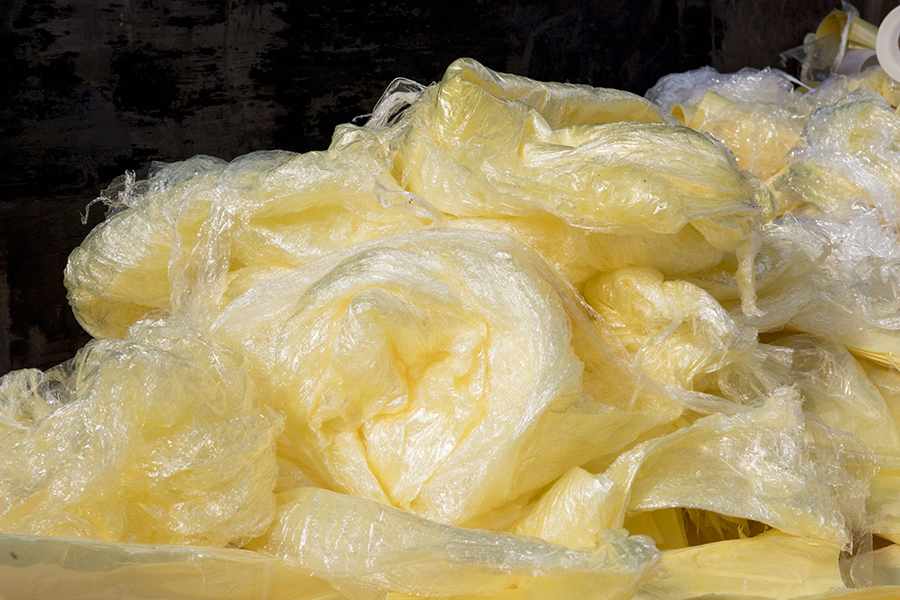
Julia and Jordy had the motivation and some startup capital: They secured a $534,760 AUD grant from Australia’s Advanced Manufacturing Growth Centre in early 2020 and raised $75K from angel investors. What they lacked in manufacturing knowledge, the then four-person team made up for with enthusiasm and patience. Trying to build an extruder and make cling wrap without instructions brought a lot of “‘What have we done?!’ moments,” Kay recalls. But after three weeks, the pilot factory was ready to go.
In order to scale production, Great Wrap needed investors. They originally sent out pitch decks through Google Drive, but “we couldn’t really get any sort of analytics [on] what people had seen,” Kay explains. “[And] you can sometimes share a whole folder by accident, giving away years of IP.”
An angel investor-turned-mentor suggested they use DocSend for their data room (a space where confidential information can be stored and shared) in 2021.
“We’ve got over 50 impact-aligned investors all around the world that we’re able to share data with really easily now,” Kay says. “You can isolate those classified documents and give access directly in a way that’s far more easy to control than a Google Drive.”
Using DocSend gave Great Wrap the security and intel they needed, as it also showed which investor read what parts of the pitch deck and for how long. They ultimately raised $24 million in their 2022 Series A funding round.
Wrapping up a global problem
What started as a thought experiment between two people falling in love is now a world-first product that could very well solve one of the largest ecological problems of our time.
“It’s hard to zoom out and think of it in that way,” Kay admits. “When you get into that mindset of constantly improving, you don’t [say] ‘We’ve done it!’ as much as you probably should.”
But as Kay pulls up to their manufacturing facility, she lets a little bit of marvel escape. “It’s the size of two football fields,” she says.
The transition to the 11,000-square-meter space was inevitable: “What we could have made in a year at the pilot factory, we can make in a day here.” (Before it produced 100,000 rolls of Great Wrap daily, the factory made plastic coolers, a bit of irony that isn’t lost on Kay.)
Thankfully, setup was easier this time around: An engineering team came in to install the extruder and the Great Wrap team has grown to include manufacturing experts.
"“We’ve got over 50 impact-aligned investors all around the world that we’re able to share data with really easily now."
“Our Head of Operations was communicating really closely with our machinery supplier in Europe,” says Kay. “They were sharing drawings via Dropbox to work through that design process, transferring huge 3D models and things like that.”
Although they now have the capacity to meet a large portion of Australia’s cling and pallet wrap needs, the factory is nowhere as large as Great Wraps’ ambitions. Jordy and Julia plan to use their latest funding infusion to commission a PHA (a type of biopolymer) biorefinery. When it’s done, it will be the biggest of its kind in the southern hemisphere, manufacturing 30,000 tons of wrap.
This year a major store expressed interest in using Great Wrap and mandating that all of their suppliers do, too. The retailer’s influence is so massive, Kay says, it would move an entire market, creating demand for plastic alternatives and changing shipping’s recycling waste stream.
Now parked, Kay steps out of her car and turns the video on. As she walks toward the factory, bright blue sky behind her, she talks about the work Great Wrap is doing through Great Lab, their research, innovation, and technology arm. Although she was demure earlier about celebrating past wins, she gets animated when discussing the future. They’re working on a new marine-degradable biopolymer made from the heat-trapping greenhouse gas CO₂, attacking climate change and plastic pollution at once.
“If we had a manufacturing partner that was using Great Wrap’s plastic alternative [that did that] in every continent of the world,” she says, “that’s success to me.”
Sounds pretty great to us, too.